It is generally known which weighing systems are available for the industry and from which companies they can be purchased. Nevertheless, in many cases unsuitable scales are purchased for various reasons.
Knowledge of scale construction is often surprisingly low. This applies not only to business people, but also to technicians. This is by no means a reproach, but is due on the one hand to the fact that technical colleges generally deal little or not at all with the construction of scales, and on the other hand the presence of the calibration stamp has a suggestive effect on the buyer. Certainly, many decision-makers have good judgment based on practical experience; however, this is offset by the large number of people who are faced with the same decision without having this experience.
The decisive factor when purchasing a scale must always be the purely commercial point of view, technical aspects are subordinate to this. As paradoxical as it may seem at first to discuss such a question at all at this point, it is nevertheless necessary; because all too often, purchasing from a commercial point of view is understood to mean merely procuring goods at the lowest possible price!
This is particularly dangerous when buying a scale because – as already mentioned – the calibration stamp can easily lead to false conclusions. The presence of the verification stamp is a matter of course – nothing more.
The calibration stamp only proves that the calibration regulations have been complied with during calibration, but offers no guarantee whatsoever that the product will function properly in the long term.
Unfortunately, there are manufacturers and trading companies whose principle is to sell their products as cheaply as possible, but who have no sense of responsibility for their products once they are in use.
These products also often receive the calibration because they were initially “trimmed” well.
In addition, the difficulties involved in manufacturing modern scales are generally greatly underestimated. Even Ruf technicians consider this production to be very simple. Many companies have been involved in the manufacture and trade of scales in recent years. Just as many of these and also long-established companies have given up or had to give up in recent years. Year after year, considerable resources are sacrificed by companies that are not involved in this line of business and have taken up this branch of production again, misjudging the difficulties of scale manufacturing.
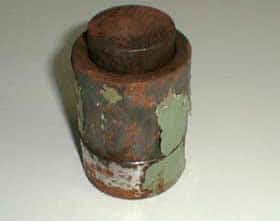
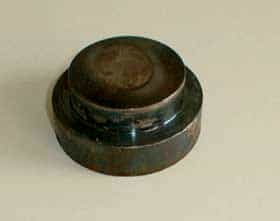
Right: Pressure piece from a truck scale from ESSMANN | Waagen & Automation, after approx. 3 years of use. Apart from the usual signs of rolling, there is no wear. Maintenance or replacement of the parts is not necessary.
These facts make it necessary to check the following criteria before investing in a scale:
- What type of goods are being weighed?
- What are the minimum and maximum loads of the items to be weighed?
- How many daily or hourly weighings are possible?
- What accuracy must be used for weighing?
- What mechanical loads are to be expected when applying the load (especially with platform scales)?
- Should the scale be installed outdoors or indoors, permanently installed, mobile, portable or relocatable?
- How is the further processing of the weighing data planned?
- What are the environmental conditions (are influences from gases, vapors or acids to be expected)?
- What are the ground conditions (for vehicle and rail vehicle scales)? Is a deep foundation (bearing on piles) and a water pressure-tight design of the foundation trough necessary?
- Is the installation location (especially for truck and rail scales) at risk of lightning strikes? In this case, is comprehensive mains-side overvoltage protection and insulation of the load cells against step voltage from the ground required?
There is no doubt that the vast majority of scales are subject to constant heavy use. The other requirements will also usually be such that only scales of high quality can be considered. If an enterprising buyer succeeds in obtaining a particularly high discount, this is only an apparent gain. However, the cheaper scales cannot generally be as good as the more expensive ones. The buyer has not been able to determine that, for example, the steel of the force transmission is inferior, the bridge or foundation construction is weaker and other properties characterize the cheaper scale as a “simpler design”. With these simpler scales
Apart from exceptional cases, significant faults and malfunctions usually occur after a relatively short time, resulting in considerable costs and trouble for the purchaser.
In any case, enormous losses can occur with heavily used scales. Scale construction experts have often carried out inspections together with operators and verification offices. It has often turned out that scales weighed several percent incorrectly and this was not noticed. The losses incurred by a company as a result of these errors amount to several hundred thousand marks a year! It is well known how much care is generally taken when purchasing other equipment, such as a motor vehicle. The prospective buyer is not satisfied with the attractive appearance of the car, he informs himself about all other details and in particular about the reputation of the supplier, takes test drives and makes enquiries, e.g. with acquaintances who have this make in use. Testing the scales is only possible to a certain extent. Therefore, the reputation of the scale manufacturer in question and corresponding references still offer a better guarantee than the best advertising and the lowest price.
This applies not only to weighing systems that are located outdoors, but also to a certain extent to those in enclosed spaces, as the strong changes in temperature and the water content of the air can have a very detrimental effect if the weighing technology is not sufficiently protected. The risk of premature failure of the most important components of the scale is even greater in the event of lightning strikes and in applications where the effects of gases, vapors and acids are to be expected. This requires not only good insulation and encapsulation of the weighing technology, but also the use of special materials. The more a scale meets these different requirements, the more expensive the one-off purchase price will be, but the lower the losses and maintenance costs will be.
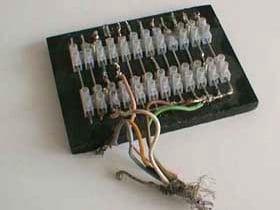
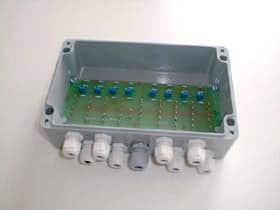
Right: Calibration board in a terminal box (IP 65 – water pressure-tight) from ESSMANN | Waagen & Automation. The connection points are clearly labeled on the circuit board so that any troubleshooting can be carried out easily by a third party. The adjustable resistors make it possible to quickly adjust the load cells to each other.
In practice, every operator will have their scale(s) checked and, if necessary, repaired by a specialist company before recalibration in order to avoid returns or decommissioning by the Weights and Measures Office. The lower the quality of the scales, the more expensive the repair will be. If you now consider that the owner of a scale wishes to have it in operation for several decades, but recalibration takes place every two or three years, you can again calculate the large losses that arise if a low-value scale is purchased with regard to the low purchase price.
For the same reason, a large number of companies have already started to have their scales continuously monitored by a scale manufacturer. In the case of frequently used scales, this is generally done at six-monthly intervals. This prevents major sources of error from occurring – without being noticed – and expensive repairs being required later. Furthermore, the availability of the systems is significantly increased.
When placing the goods to be weighed, e.g. on a platform scale, an impact load is to be expected: The scales must therefore be able to withstand loads that are practically much higher than the weighing load and must be manufactured accordingly. The nature of the ground, for example, usually requires a significant deviation from the normal design when installing truck scales in rocky or swampy terrain. With regard to these special requirements, the specialist knowledge of the manufacturer in question must always be taken into account during procurement.
In recent years, manufacturers have often given customers the software for recording weighing data as a gift when they buy a scale.
Here, the buyer should ask himself what motivation the manufacturer should have to provide support for this product or to guarantee the delivery of updates. In any case, special attention should be paid to the software on a scale. The decision-maker should ask himself how a pure software company can be familiar with the weighing functions and the technical verification regulations. Here, the experience of the scale manufacturer from many cases of need is invaluable for the user. Only the flexibility and thus the simpler expandability of the software as well as the basis on common operating systems, databases and development environments creates investment security here. Furthermore, the decision-maker should ensure that there is a central point of contact for the support of weighing technology and software and that remote maintenance is possible. The scale manufacturer should also have its own software department with trained specialists.
The reputation of the supplier and corresponding verifiable references should be decisive for the procurement. With regard to the software, you should always ask for a demonstration or expect to be provided with a test system. It is almost impossible to make a correct decision based on information on paper or a self-running demo program.
To summarize:
- Check carefully whether the scales on offer are fit for purpose in every respect.
- Only buy from companies that are recognized as doing a good job and have appropriate references.
- Interested parties should first check whether products from domestic companies might be more suitable for their business, as the quality requirements abroad are often different or subject to different standards.