Salt silo with continuous scale for road salt
Continuous scales are one of the most versatile measuring instruments on the market. Thanks to their compact design and versatility, they are used in many industries. The integration of a continuous scale in a salt silo makes it possible to continuously monitor the contents of the silo and precisely dose the discharge quantity.
Road salt from the salt silo
Road salt is an essential component of winter road maintenance. In Germany, around one million tons of salt are used on the roads every year. Most of the salt comes from abroad or from the Ruhr area and is often delivered in ships. It is removed from these ships using conveyor technology and stored temporarily in large warehouses. The salt is then distributed to the winter services in Germany by truck or rail. To do this, it must first be filled into large salt silos. From these, the de-icing salt is then loaded into the vehicles in suitable quantities using continuous scales.
The requirements for a salt silo
A salt silo is a warehouse for de-icing salt that is used to prevent ice and snow on roads and sidewalks. It is usually equipped with a continuous scale that enables the material to be loaded quickly and efficiently. The design of the silo should be such that dry storage of the material is guaranteed.
The requirements for a salt silo are therefore relatively clearly defined: It should be large enough to hold a large quantity of de-icing salt, it should be watertight to protect the material from getting wet, and it should have a continuous scale to enable a quick and efficient loading process.
Another requirement that is often placed on a salt silo is compatibility with different types of road salt loading equipment. As most loading operations are mechanical, it is important that the silo is equipped with the appropriate connections and devices to ensure a smooth process.
Why a wooden silo?
A wooden silo offers a number of advantages over other construction methods. The high insulating properties of the material ensure that no condensation occurs in the silo. Wood is also a naturally UV-resistant material, making it ideal for outdoor use. The capacity of wooden silos is usually between 35 and 600m3. Wooden silos are characterized by low service and maintenance costs, as they do not require regular protective coatings.
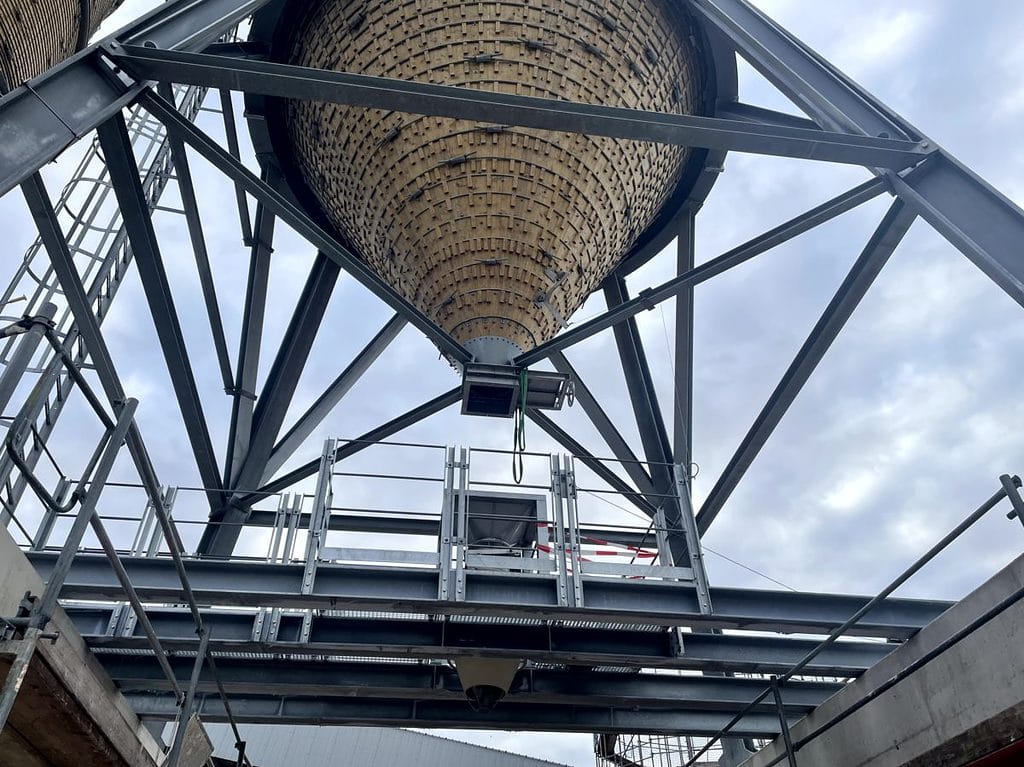
Why a GRP silo?
A GRP silo is the best choice for storing road salt as it has a long service life, mirror-smooth inner surfaces and is corrosion-resistant. It is also low-maintenance and chemically resistant. In addition, it offers high thermal insulation, making it an ideal choice for storing de-icing salt in cold climates. The capacity of GRP silos is usually between 25 and 300m3 . Another advantage of this design is its relatively low weight.

How a continuous scale works
A continuous scale is a measuring device that measures the amount of material flowing through a process. This type of scale is often used in the bulk materials industry to monitor the amount of product or raw materials flowing through a factory or warehouse. Most weigh-through scales are computerized and can be connected to other machines and systems. Continuous weighers are also commonly used in the food industry, in the production of pharmaceuticals and in the chemical industry. They can also be used in other areas where it is important to know the quantity of materials flowing through a process. Continuous weighers are usually very accurate and can be used in many different environments.
Hopper scales usually consist of a pre-hopper, a weighing hopper and a post-hopper. The weighing hopper is filled with the bulk material using a conveyor system – such as a screw conveyor or belt conveyor – while the pre-hopper remains open.
When a specified target weight or time is reached, the pre-hopper is closed. The weighing hopper is then weighed precisely and the weighing result is stored and evaluated in the weighing terminal. The special flap geometry then enables the weighing hopper to be emptied quickly.
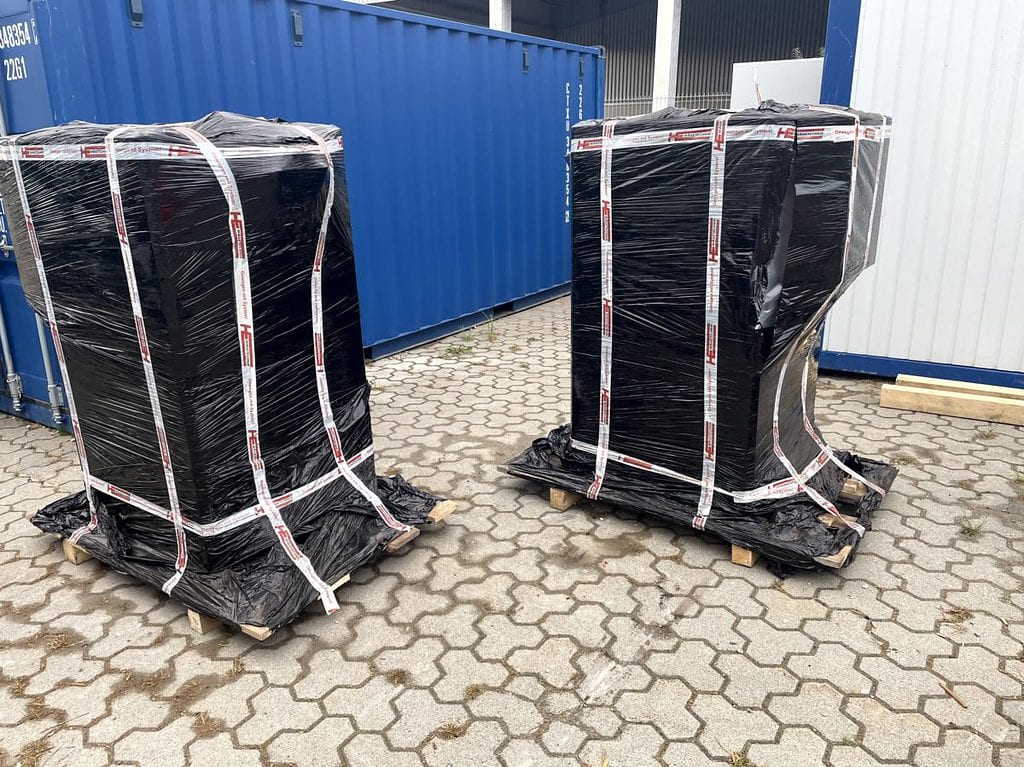
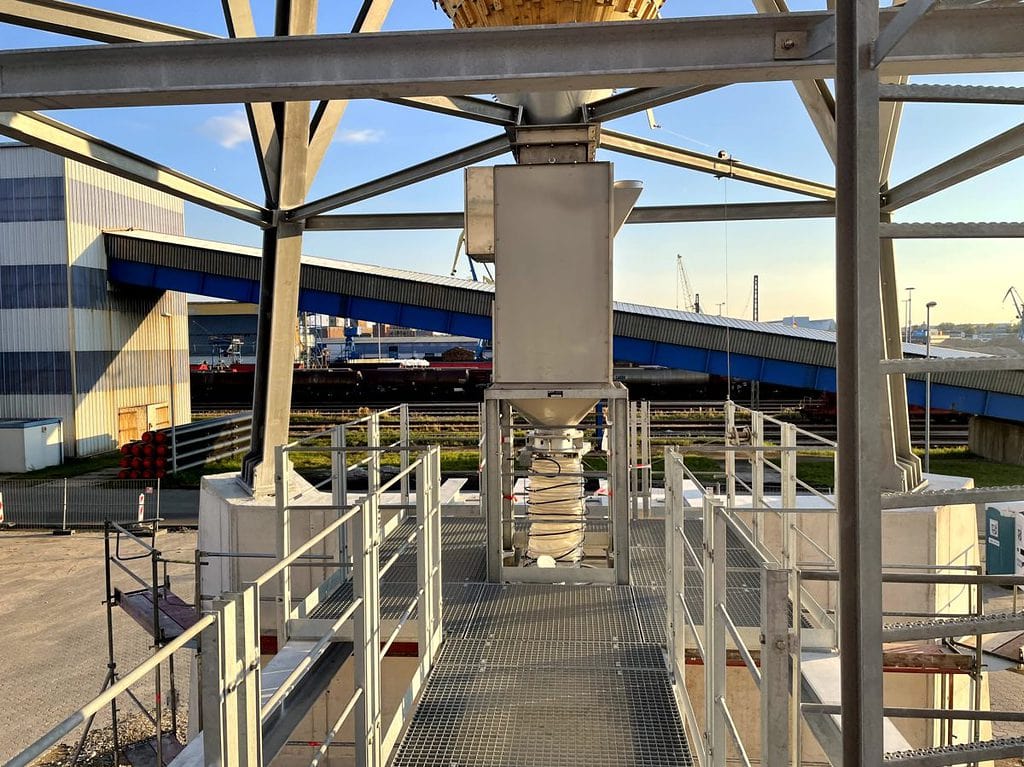
Why a continuous scale for road salt makes sense
A salt silo with a continuous scale is the ideal solution for companies that regularly deliver de-icing salt to their customers. The scale prevents trucks or wagons from being overloaded and enables precise dosing of the de-icing salt. The calibrated handling scales also allow the de-icing salt to be invoiced according to actual weight, thus ensuring greater transparency in the supply chain. The scales also make it easier to check the fill level of the salt silo.
When using a continuous scale for road salt, there are a few points to consider in the design. For example, the components inside the scale must be explosion-proof, and a stainless steel design is recommended due to the high abrasiveness of salt and for corrosion resistance.
Overall, the issue of steel rusting under the influence of salt should not be neglected. The chemical process of corrosion by oxygen corrosion of a metallic material takes place under the influence or consumption of oxygen, i.e. oxygen acts as an oxidizing agent. To prevent corrosion of steel components, alloys are therefore produced with metals that are more noble and form a stable oxide layer (stainless steel).
Advantages of a salt silo with continuous scale
- Protection against overloading of trucks and wagons
- A salt silo with a continuous scale prevents expensive overloading of trucks or wagons, as the scale precisely checks the fill level in the truck or wagon. If the truck or wagon is reweighed on a checkweigher, this ensures that it is not overloaded and that the transporter or filler does not incur high fines.
- Invoicing possible
- A calibrated handling scale enables the road salt to be invoiced.
- Level control and dosing
- The salt silo with continuous scales enables the fill level to be checked and the de-icing salt to be dosed precisely.
The salt silo is ideal for transshipment companies and transshipment ports that regularly deliver road salt to different customers.
Disadvantages of a salt silo with continuous scale
- Higher investment costs
- A salt silo with a continuous scale usually costs more than a conventional silo. This is due to the increased cost of the scale itself as well as its installation and maintenance. It is therefore important to obtain precise information in advance and weigh up whether the additional price will actually bring the expected benefits.
- Possibly slower filling
- Another disadvantage of a salt silo with a continuous scale is that filling it is usually somewhat slower than with a conventional silo. This is because the scale must first be set to the correct value before the salt can be poured in. In addition, the salt must be reweighed at regular intervals to ensure that the displayed values are correct. It is therefore important to allow sufficient time when planning the filling process.
- Calibration costs
- Another disadvantage of a calibrated continuous scale is the fact that it has to be calibrated regularly. This not only means additional costs for the operation of the salt silo, but also for the maintenance and care of the scale itself.
Application example for the continuous scale under a salt silo
The seaport of Wismar is one of the most important seaports in Germany. Millions of tons of goods are handled here every year. Efficient scales are required to handle these goods. ESSMANN | Waagen & Automation has been supporting the seaport of Wismar for decades and has supplied dynamic rail scales, truck scales, transshipment scales and belt scales over the years. In the latest project, ESSMANN | Waagen & Automation, together with the company HOLTEN GmbH & Co. KG, supplied and commissioned two salt silos with continuous scales. The continuous scales are able to process large quantities of salt and thus efficiently handle the operation even at peak times.
Project planning phase Salt silos with continuous scales for de-icing salt
In the project planning phase of a salt silo with continuous scales, it is important to precisely calculate the size of the silo and the scales. In addition, the loading routes and routes must be carefully planned in order to ensure optimum handling of the trucks.
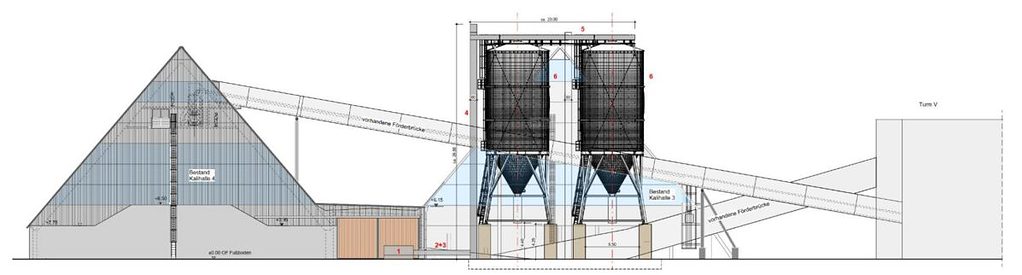
Assembly of the salt silo with continuous scales for de-icing salt
The installation of salt silos with continuous scales is relatively simple and can usually be carried out by a specialist company. However, the ground must first be prepared. In many cases, explosive ordnance soundings are required, as the foundations can be very deep due to the size of the system. Pile foundations may also be necessary.
The foundation must be absolutely stable, as the silos have a high weight and are exposed to very high loads in strong winds or snowfall. Once the foundations have been laid, the assembly of the system can begin. As a rule, several modules are supplied, which are assembled on site.
The scales must be installed so that they are positioned exactly under the silo outlet. It is important that the scales do not vibrate and are decoupled accordingly, otherwise the measurements will not be accurate. Once the scales have been installed, the salt is filled into the silos. As a rule, this is done using a box system or excavator.
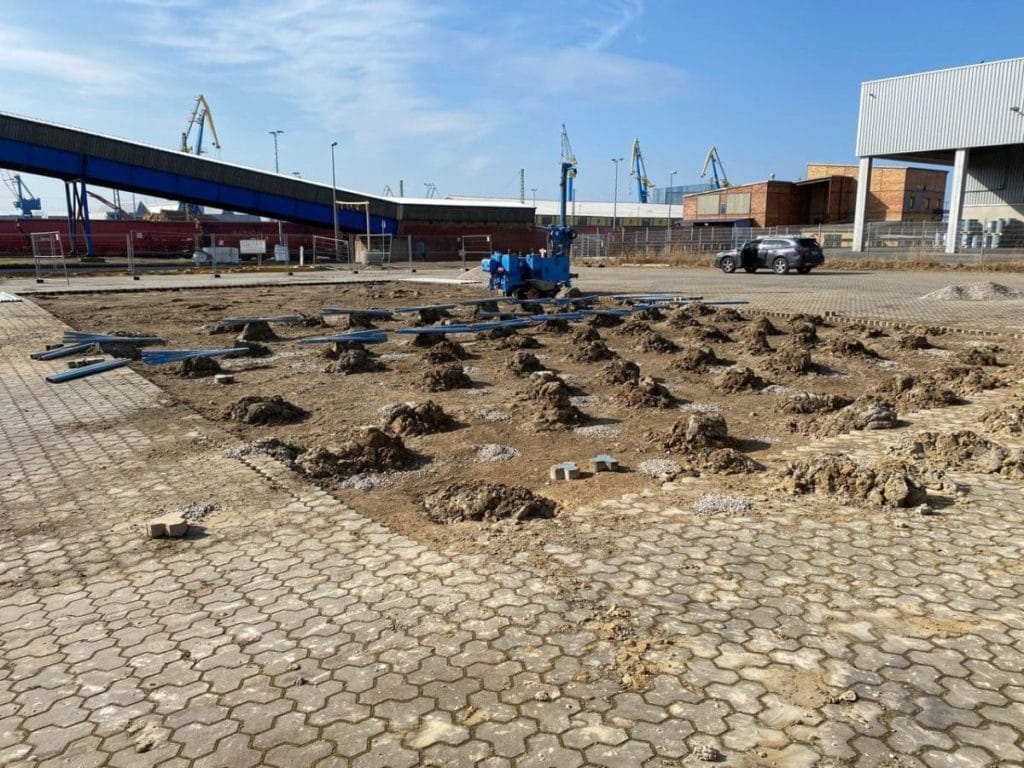
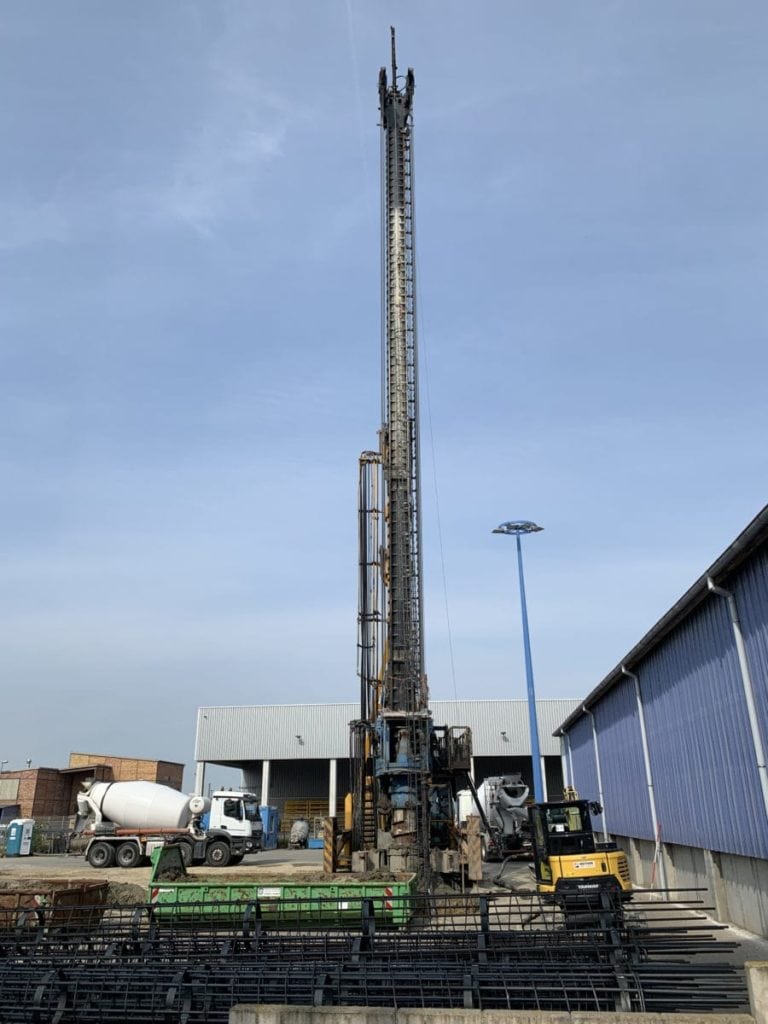
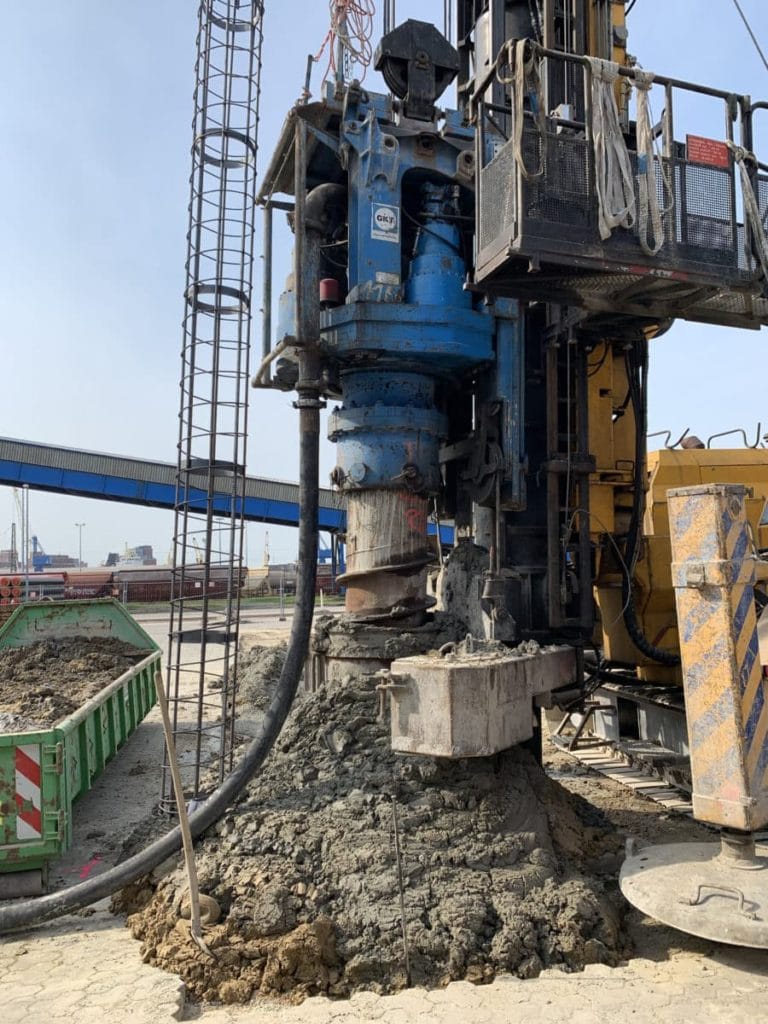
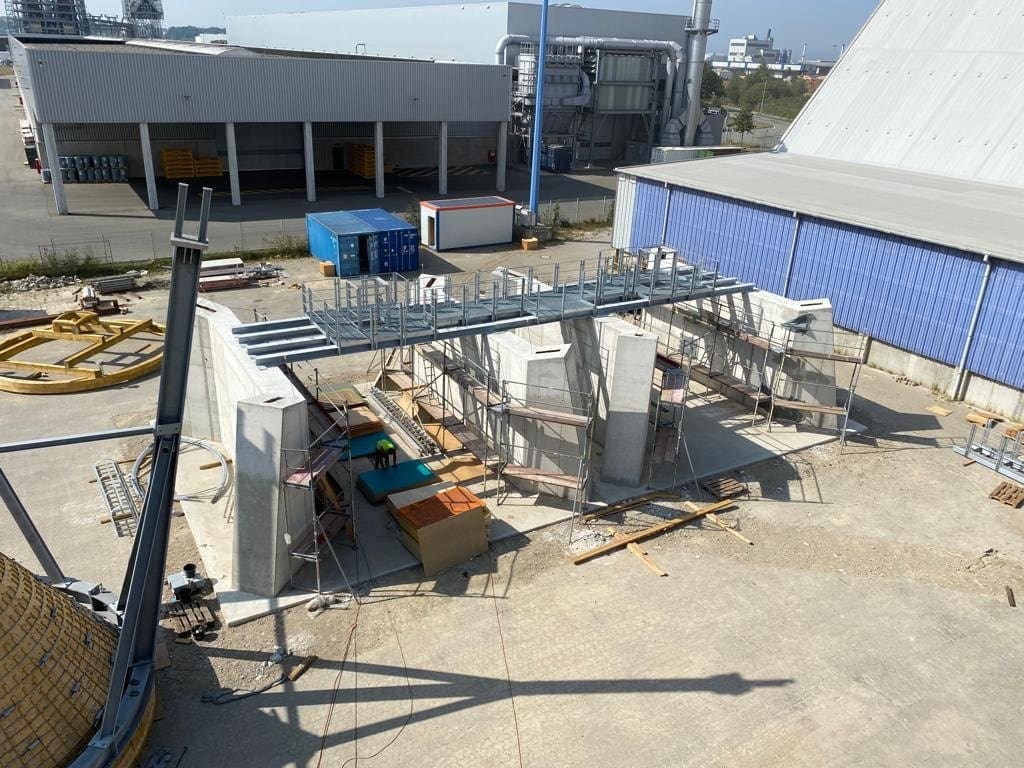
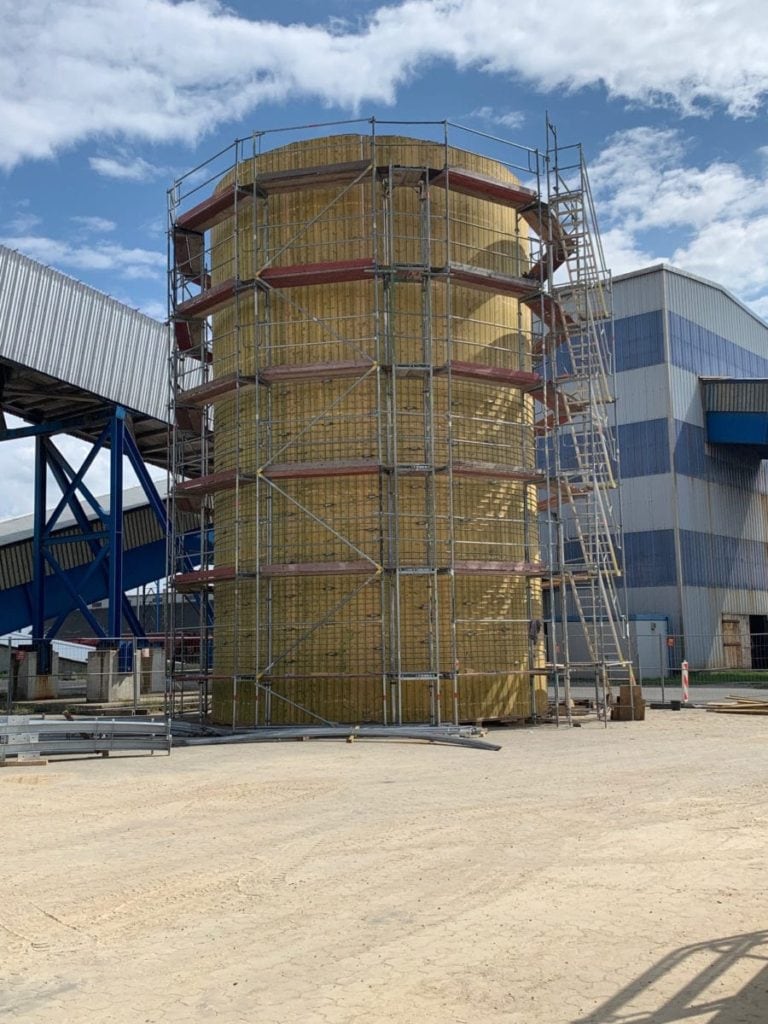
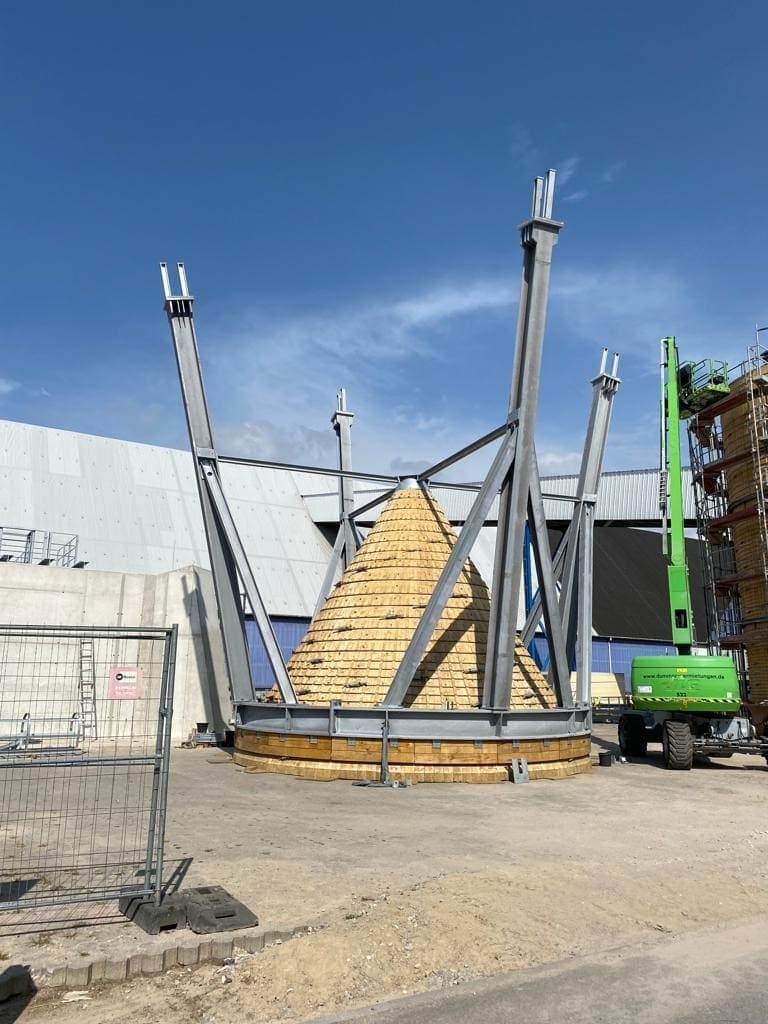
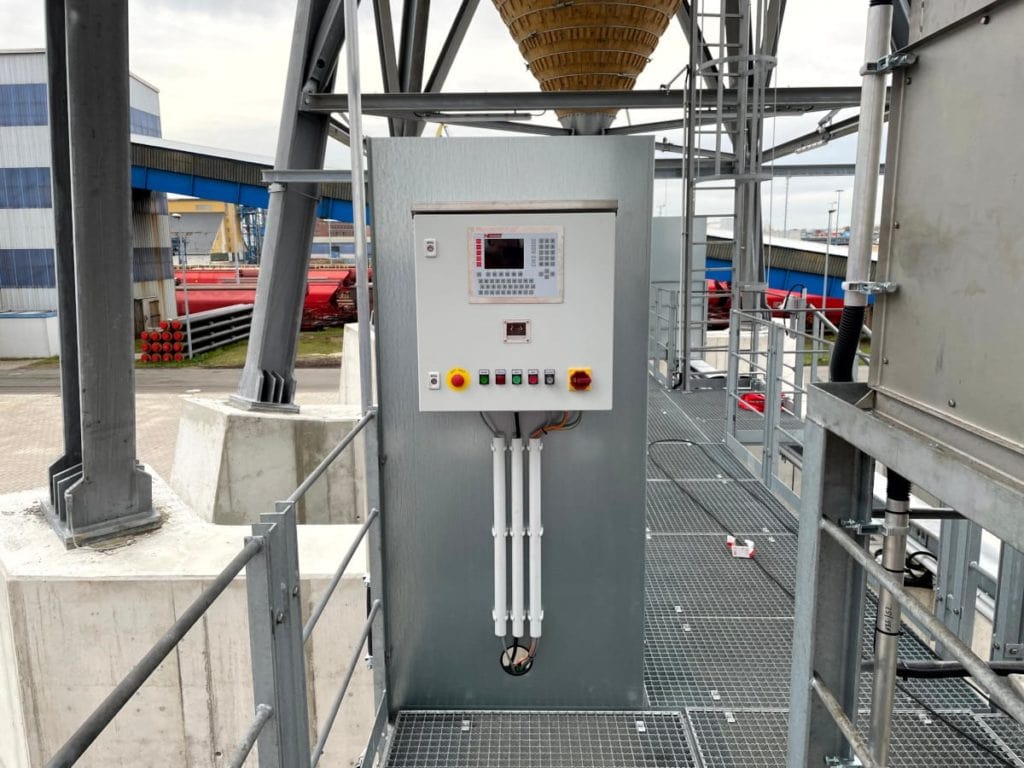
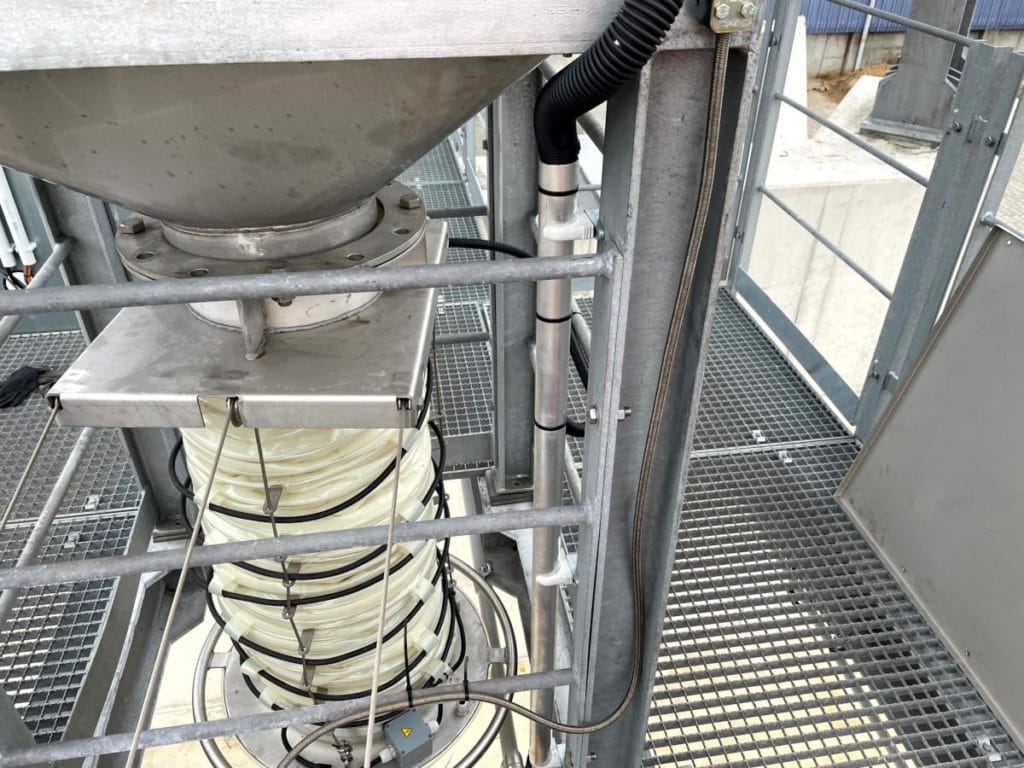
Commissioning the continuous scales
Commissioning the scale with de-icing salt is an important step to ensure that the system works properly. First, the electrical cables and pneumatics are connected correctly according to the plans and specifications of ESSMANN | Waagen & Automation.
The silo is then filled with sample material and the outlet slide above the continuous weigher is opened. The continuous weigher is tested in trial operation to ensure that all signals switch correctly and the weighings are accurate. For this purpose, the dosed de-icing salt is reweighed on another truck scale and the weighing results are compared.
The connection to the IT system landscape takes place in the next step. ESSMANN | Waagen & Automation has its own IT department for this purpose, which works together with the customer on the integration.
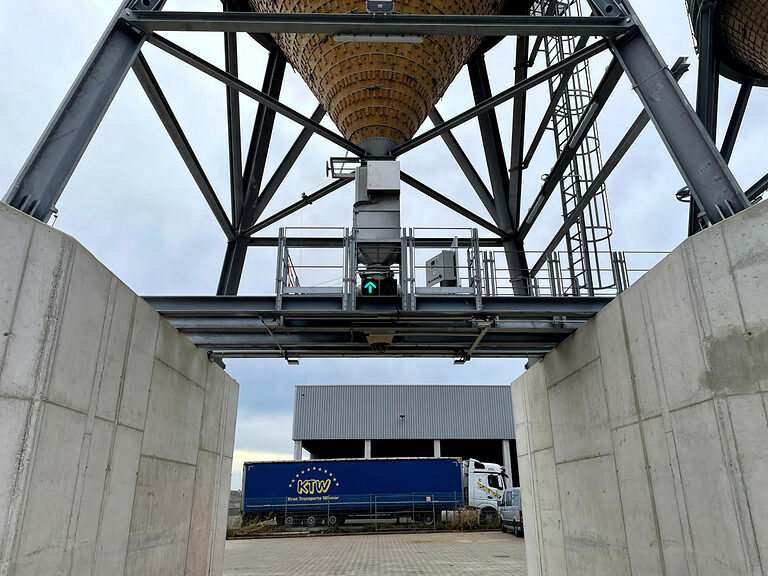
Loading process sequence
- Registration of the driver at the entrance gate with order confirmation / delivery bill with barcode. This contains a transport number. In addition, the seaport of Wismar has a registration system with a time slot booking system in order to organize the truck flows on the port premises as efficiently as possible.
- Drive to the salt silo with continuous scale.
- Preparation for loading: The truck driver positions his truck under one of the two salt silos. To simplify matters, traffic lights (red/green) are attached to the salt silos to indicate any malfunction of the silo or if the fill level is too low.
- Authentication and release of dosing: The driver holds his delivery bill in front of the self-service terminal from ESSMANN | Waagen & Automation and the continuous scale is released. For this purpose, a mutual electronic data exchange takes place in advance, which only allows operation by registered drivers at the self-service terminals.
- Start loading: The driver enters the desired loading quantity.
- Stop the loading process: The driver can manually stop the process, for example when changing the dome cover.
- Completion of loading: As soon as the total quantity has been reached, dosing is stopped automatically.
- Driver log-off: The driver logs off and the delivery bill is printed. A report on the dispatched trucks is also generated automatically.
How to choose a salt silo with a continuous scale
If you want to buy a salt silo with a continuous scale, it is important to consider a few factors. First of all, you should decide what size or capacity the silo should have. Most companies need a silo that can hold several tons of salt. If you are a smaller company, a smaller silo may be sufficient.
It is also important to find a supplier that provides a high quality continuous scale. There are many different types of scales on the market, and you should make sure that the scale you choose is accurate and reliable. A high-quality scale is very important as it will help you determine the amount of salt you want to put in your silo.
You should also make sure that the software you use for your scale is easy to use. Many scales are very complex and have many different functions. It’s important to make sure you understand and can operate the software so you don’t waste time trying to figure it out.
Advice is very important when choosing the right salt silo with continuous scale. If you have any questions about the different options or need help choosing the right silo or scale, please contact us. We will be happy to help you plan and select the right silo and scale for your company.
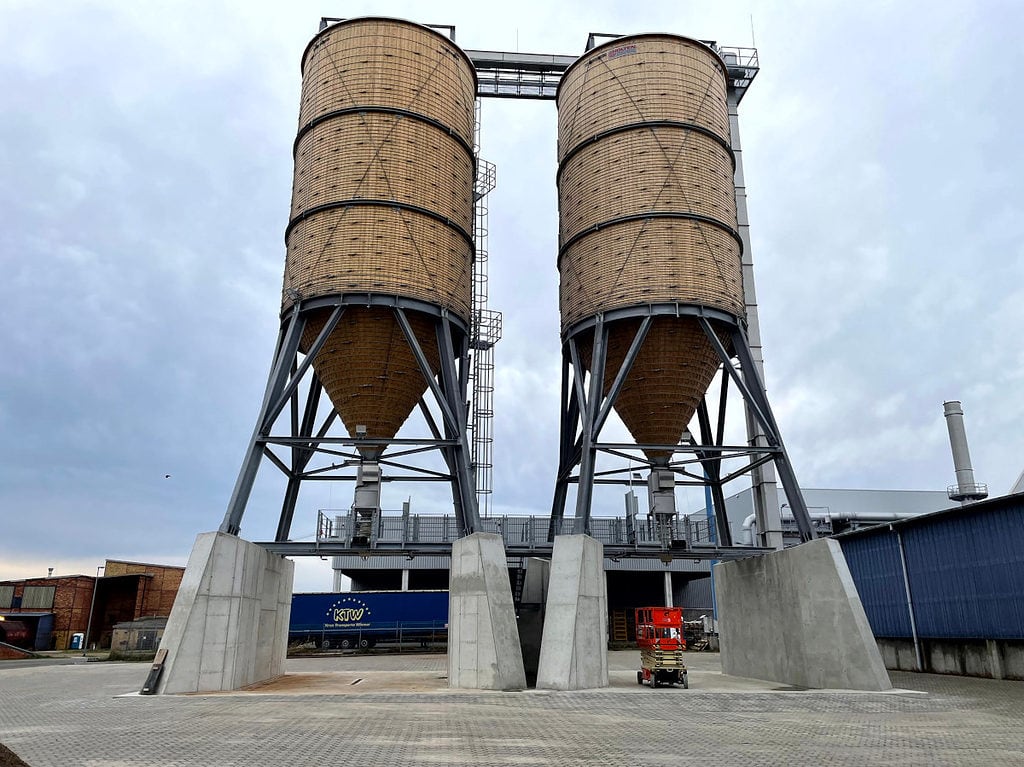