Digitalization and AI in the Port of Hamburg
Digitalization offers numerous opportunities to increase efficiency in ports. They range from the collection and storage of data to the loading planning of ships and the simulation of the entire terminal processes. In the event of ship delays or breakdowns, digitalization not only enables rapid rescheduling, but also replanning of the inflow of vehicles and goods. This means that the limited storage space at the terminal can be optimally utilized.
The Hamburg research project AKIDU aims to increase the competitiveness of German seaports by comprehensively developing the storage and handling system for rolling cargo. The aim is to use the possibilities of digitalization and artificial intelligence (AI) for non-standardized RoRo goods.
Focus on RoRo cargo
RoRo stands for “Roll on Roll off” and refers to a process in freight shipping in which the cargo is driven onto a ship under its own power without any additional equipment and then driven off again during unloading. This transportation system is mainly used for rolling cargo such as cars, trucks, buses, agricultural vehicles or even rail vehicles.
RoRo ships have decks that can be driven on and onto which the cargo can be rolled. These decks are often adjustable in height, which enables flexible use of the cargo space. The advantages of the RoRo method are short handling times, gentle cargo handling, simple port infrastructure and flexibility in the composition of the cargo.
It enables fast and efficient loading and unloading, minimizes damage to cargo thanks to safe and controlled handling and is cost-effective thanks to optimized use of space and time in ports and on ships.
The AKIDU project focuses on RoRo cargo, in particular non-standardized project cargo. In the sub-project “3D measurement and identification of goods using AI”, the Hamburg IT Technology Center (HITeC) will specify the sensor technology for measurement and develop machine learning methods for the classification of goods, attachments and superstructures as well as damage based on the sensor data.
Truck scales for the test facility
For the test facility, the mobile and flexibly expandable truck scale ESSMANN HE-TS is used. Trucks are weighed on it and simultaneously measured volumetrically using cameras and sensors. The data obtained is used to develop an AI-supported loading optimization system for ships. The aim is to increase the handling capacity of the port terminal in this way.
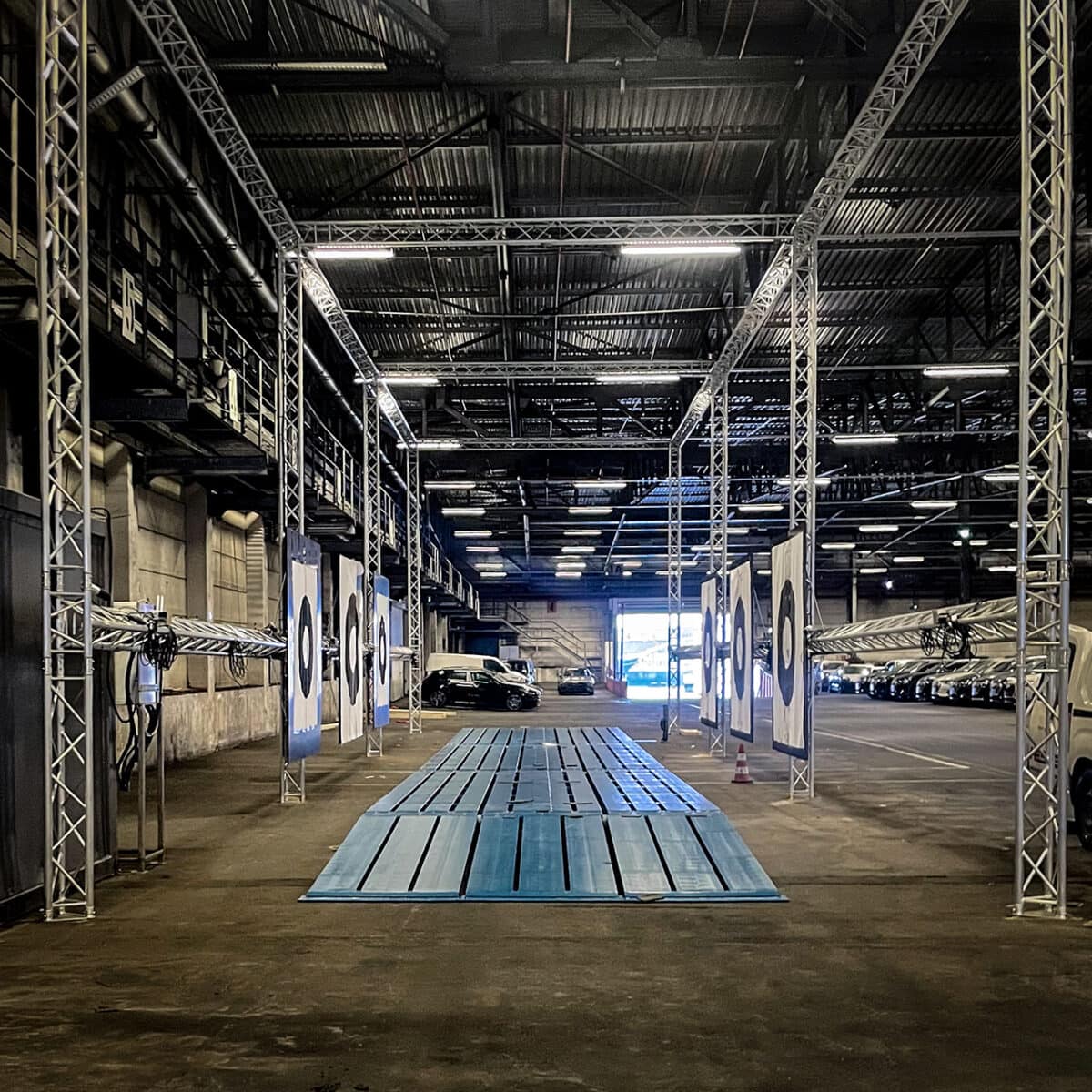
Partners and promotion
In addition to HITeC, akquinet port consulting GmbH (apc) and Unikai Lagerei- und Speditionsgesellschaft mbH are also partners in the project.
The project is supported by the Federal Ministry for Digital and Transport Affairs (BMDV) as part of theInnovative Port Technologies (IHATEC II) funding program.
Overall, the AKIDU project represents an important step towards a digitalized and AI-supported future for German seaports. We are delighted to be part of this research project with our truck scales. If you would like to find out more, you can find an interview with AKIDU project manager Stefan Henke from Akquinet here.
History: 1st volume measuring device in the 1990s
The ESSMANN team is particularly pleased about this application, as it closes a circle: the first type-approved and calibratable volume measuring system for road vehicles in Europe was developed by ESSMANN Wägetechnik for the Sassnitz-Mukran ferry port in 1998. By using laser scanners and an underfloor vehicle scale, the length, width and height of the vehicle could be determined in addition to its weight. The data obtained helped the loading personnel to distribute the freight on the ferries.
The system is still in operation today at the Mukran ferry port, but has since been decommissioned.
