Platform scales for filling gas cylinders and gas drums
ESSMANN | Waagen & Automation has developed and successfully commissioned a special weighing system for filling gas cylinders and gas drums for a customer in the gas industry.
Customer
The customer is a specialist for specialty gases. It produces gases for industry, medicine and trade. The products, in addition to gases, refrigerants and accessories, are offered to many industries worldwide.
Requirements for the gas cylinder scale and gas drum scale
Two separate scales were required for two new loading stations for gas drums and gas cylinders. On the one hand, these should be able to be installed at ground level and, on the other hand, be equipped with an individual, customized loading control system that can control the corresponding valves for loading gas.
Liquid gas is stored in pressurized gas containers (gas cylinders and gas drums) in a liquid state. This is where the name liquefied gas comes from. If such a pressure vessel filled with liquid gas is exposed to high temperatures, the liquid gas expands and the pressure increases. For this reason, all commercially available gas cylinders are designed for significantly higher pressure ratios than occur in reality under normal environmental conditions. The gas pressure in the liquid state increases by 7 bar for every 1° C. For this reason, pressure vessels must have a sufficient expansion volume, among other things. The following example applies to propane gas:
- A propane gas cylinder filled to 80% has a pressure of approx. 7 bar at an outside temperature of 15° C.
- The full cylinder volume is only reached at an outside temperature of approx. 70° C. This leads to a pressure of approx. 25 bar.
- If the temperature continues to rise, the pressure inside the bottle also continues to increase.
- For this reason, gas cylinders are fitted with a safety valve and in Germany may only be filled by specialist companies on calibrated scales.
Due to the high degree of protection, the gas cylinder scale can also be used when filling gas cylinders with a high level of condensation. The very robust design results in high accuracy and temperature stability.
The scales meet very high overload and EMC requirements. This ensures safe, error-free and accurate operation.
Technical solution
ESSMANN | Waagen & Automation hat hierfür den Kunden beraten und speziell angefertigte Waagen mit dazu passenden Fundamentrahmen und zwei EWS-8000E Wägeterminals mit Barcodeleser, angepasster Beladebedienung und -steuerung entwickelt, gefertigt und ausgeliefert.
Our scales therefore fulfill the following applications:
- Weight measurement in the industrial sector
- Level measurement of liquid gases in gas cabinets and gas supply systems
- Level measurement for chemical supplies
Production of gas cylinder scales and gas drum scales
The foundation frames of the scales are manufactured by ESSMANN | Waagen & Automation in solid construction and hot-dip galvanized.
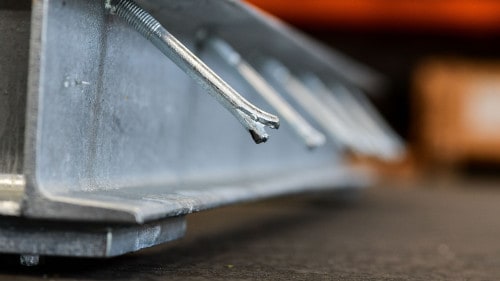
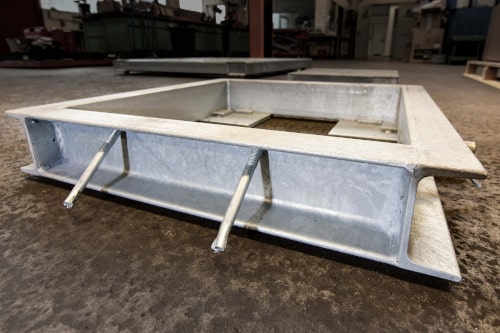
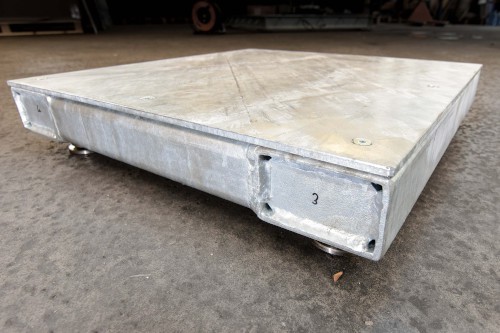
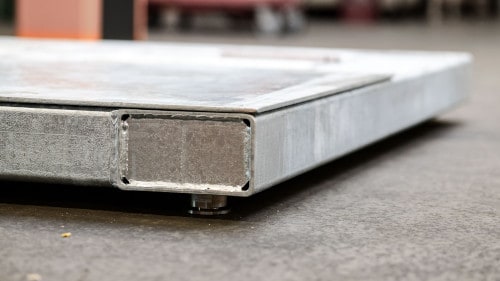
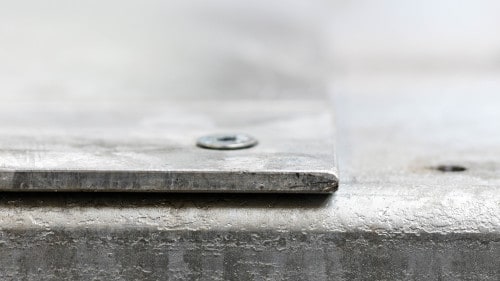
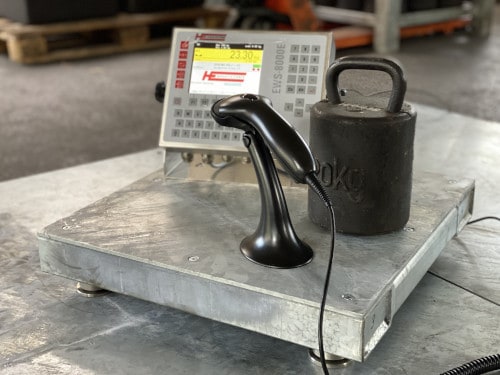
Operating the scales
ESSMANN | Waagen & Automation bietet unterschiedliche Möglichkeiten der Bedienung der Plattformwaagen an. Einerseits ist es möglich, dass die Waagen komplett automatisiert durch ein übergeordnetes Leitsystem angesteuert werden. Andererseits kann ein Bediener vor Ort mittels eines Kartenlesegerätes oder Scanners, der Wägeelektronik EWS oder einen Touchscreen-PC die Waage und den Beladeprozess bedienen.
In this case, the customer opted for coupled operation via the EWS-8000E weighing electronics with a scanner. ESSMANN | Waagen & Automation has developed its own software for the weighing electronics for easy operation by employees.
To do this, the operator first logs on to the weighing electronics. In automatic mode, the logged-in user is also checked by the external IT system for security reasons. In emergency mode, the logged-in user is checked by an internal database query.
A scale check must be carried out once a day. To do this, the “Scale check” program is selected and the user is guided through the procedure, which roughly runs as follows: a test weight is placed on the scale and the result is printed and saved. If the scale check is within tolerance, the current date is saved as the test date.
The filling process is then initiated. The outlet of the suction valve is set for this. The scale should then be unloaded. If aids are required for filling, these must now be placed on the scales. As soon as a container with a pallet is placed on the scale, the pallet weight must then be entered. Then enter the barcode of the container with or without pallet using the barcode reader.
The operator then mounts the filling head and enters the labeled tare weight of the container and starts the filling process via a context menu with several control steps.
Related products
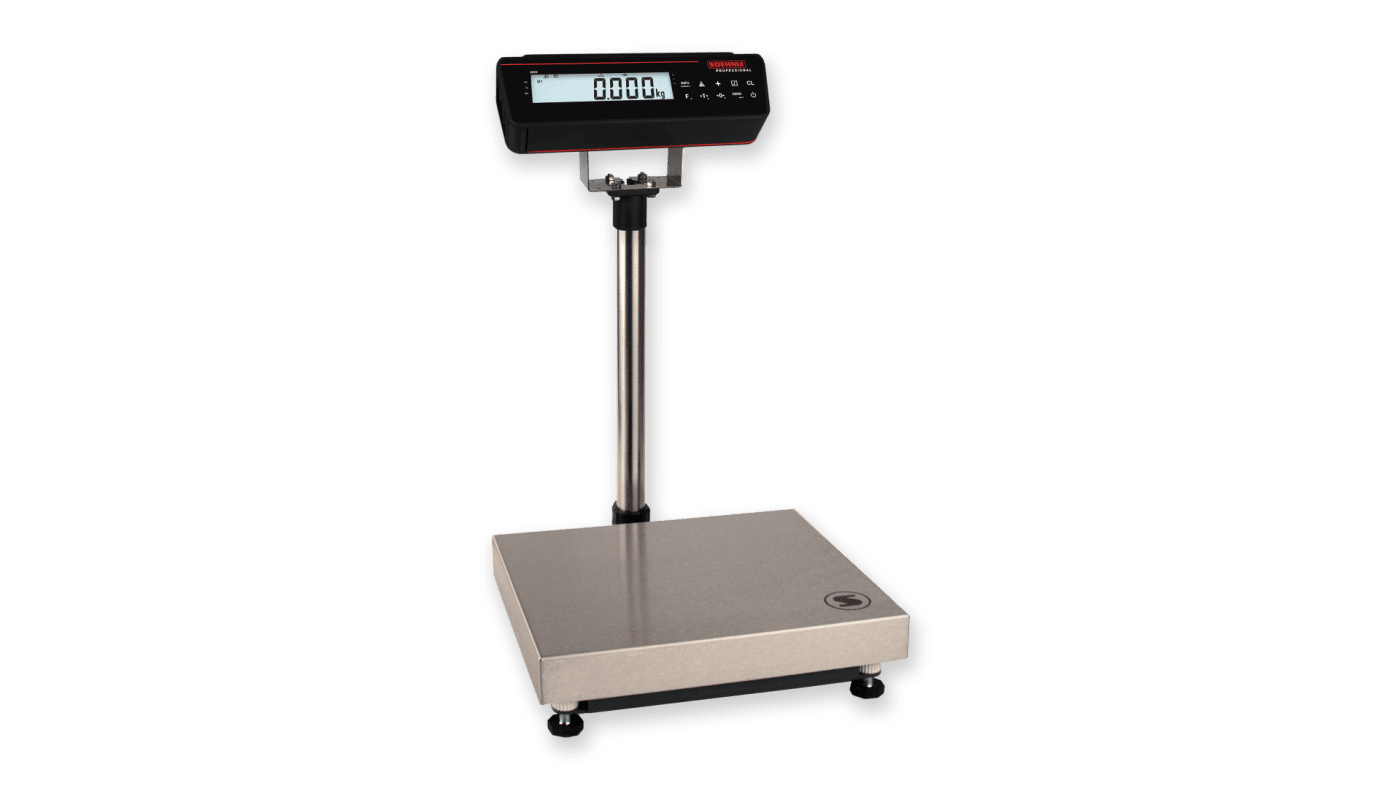
Verified platform scale Soehnle 7973.16.120 – Maximum load 150 kg – Readability 10 g – Weighing surface 660 x 550 mm – Stainless steel
Find out more in the ESSMANN scale store
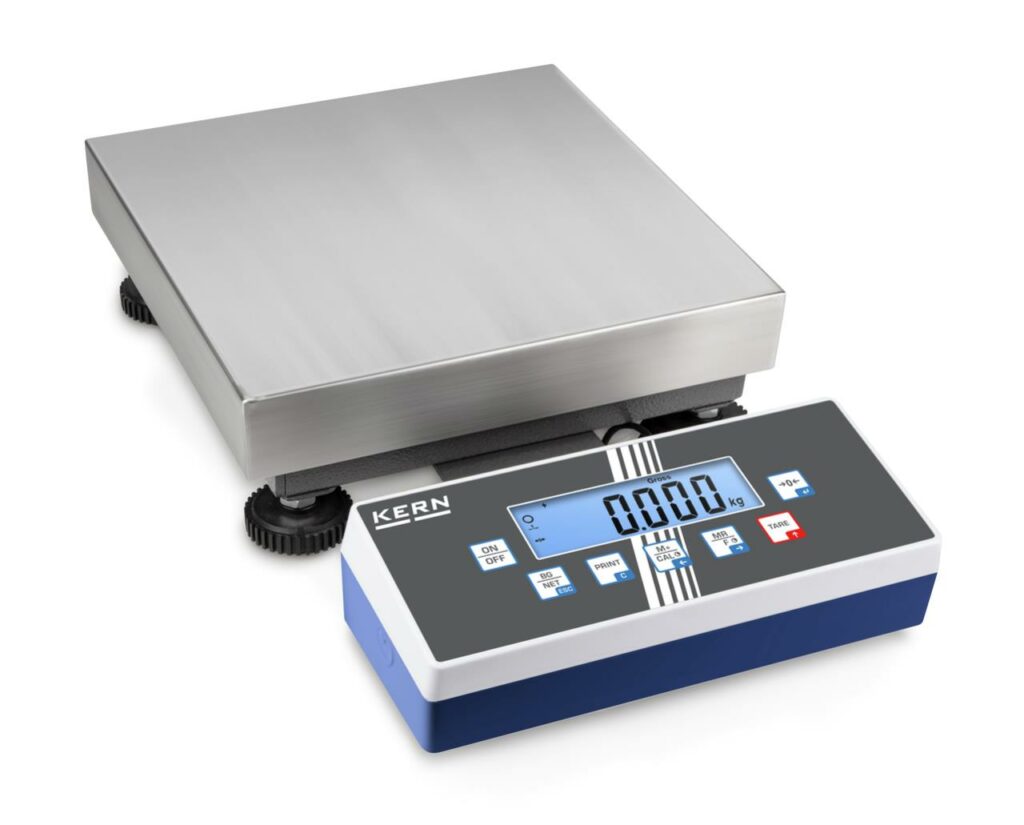
Find out more in the ESSMANN scale store
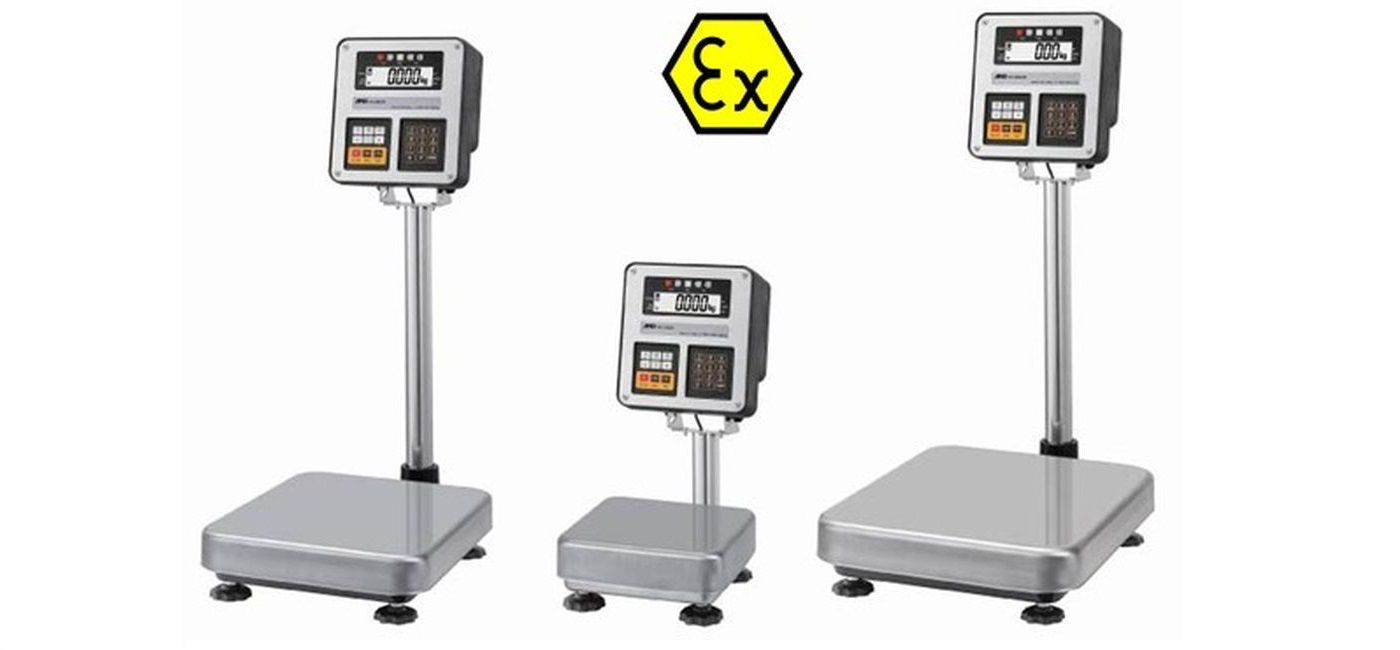
Find out more in the ESSMANN scales store